Research » Waste Treatment and Primary Metallurgy
The primary production of metals is usually accompanied by by-product residues. These residue streams are a potential problem due to environmental concerns. Contained in these residues are valuable metals in lower grades than the primary production source. The IME is seeking means to exploit these vast secondary resources for value reclamation through development of innovative processes.
The focus areas include and are not limited to the following: slag cleaning for recovery of precious metals, landfill mining to recover metals and plastics, red mud processing for recovery of high value metals such as Sc and Ga. Inertization of slags is another large research focus. Metallurgical slags can be modified so that they may be used e.g. as cement additives or as road building materials. This “zero-waste” approach contributes enormously to a sustainable metal production, which is actively propagated by IME in R&D projects and teaching.
The processing of these materials at IME is predominantly undertaken by pyrometallurgical means. The facilities at IME for processing of the aforementioned resources comprise laboratory scale and demonstration scale furnaces and converters. Activities within IME in this area include thermochemical process modelling, high temperature experiments to validate the theoretical basis.
Alumni:
- Dr.-Ing. Marcus Sommerfeld
- M.Sc. Buhle Xakalashe
- M.Sc. Christian Dertmann
- M.Sc. Jil Schosseler
- Dr.-Ing. Kilian Gisbertz
- Dr.-Ing. Jörn Böhlke
- Dr.-Ing. Florian Binz
- Dr.-Ing. Jürgen Schlimbach
- Dr.-Ing. Jackson Rodriguez
- Dr.-Ing. Daniel Schmitz
- M.Sc. Magnus Sievers
- Dr.-Ing. Ashour Owais
- Dr.-Ing. Graciela Mendez
- Dr.-Ing. Yiqian Ma
- Dr.-Ing. Christoph Kemper
- Dipl.-Ing. Erik Hecker
- Dr.-Ing. Andreas Lützerath
- Dr.-Ing. Frank Kaußen
- Dr.-Ing. Marco Zander
- M.Sc. Gunnar Hovestadt
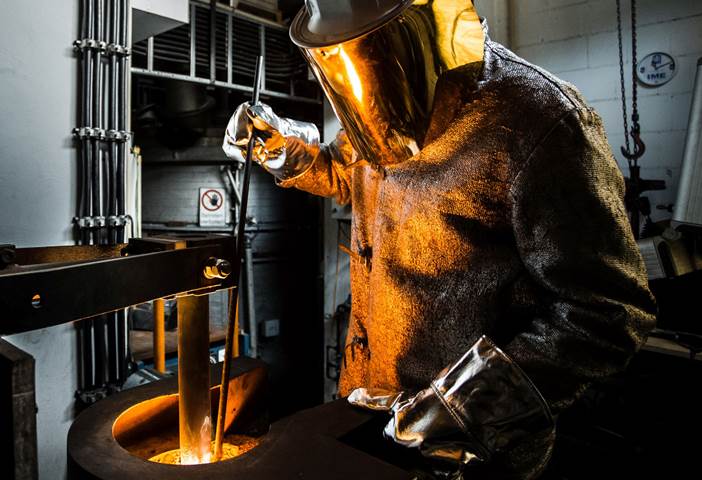
Project List
Title
SMART – Application of Artificial Intelligence for wastewater treatment processes in the West Balkans countries
Type
Verbundforschung
Sponsorship
EU
Duration
01.09.2021 – 30.11.2021
Partner
IME, RWTH Aachen – Germany; Olimpija, Uzice – Serbia
Description
The proposed artWater project establishes a vertical for the transfer of WWT (Wastewater Treatment – WWT) knowledge and technology from RWTH to Olimpija. Olimpija will integrate the transferred inputs into the artWater system based on its competences in implementing Artificial Intelligence, Machine Learning, and IoT (AI / ML / IoT) based systems. ArtWater will be applied to a use case in the Zlatibor region (City of Uzice, Serbia). ArtWater can be a key element of the WWT strategy, both in effluent quality parameters prediction, and sustainable water pollution monitoring in Serbia and surrounding countries. For Olimpija, the project increases its potential and capacity to monetize AI/ML/IoT based solutions applied to WWT. The benefit for RWTH is the enrichment of WWT theoretical models and experimental results with reliable ML models. Additionally, the RWTH benefit is the validation of theoretical knowledge in a real-world use case — WWT plant
Title
MeteoR – Mechanical-Thermochemical Process Combination for the Recycling of Fine Fractions from Waste Treatment Plants
Type
Verbundforschung
Sponsorship
Österreichische Forschungsförderungsgesellschaft mbH (FFG)
Duration
01.01.2023 – 31.12.2025
Partner
Montanuniversität Leoben – Lehrstuhl für Abfallverwertungstechnik und Abfallwirtschaft; Bernegger GmbH; FCC Austria Abfall Service AG; IFE Aufbereitungstechnik GmbH; Lafarge Zementwerke GmbH; Technische Universität Graz Institut für Materialprüfung und Baustofftechnologie mit angeschlossener TVFA für Festigkeits- und Materialprüfung
Description
The Austrian waste management industry produces about 1.9 million tons of fine fractions per year, most of which have so far been landfilled or incinerated. These fine fractions contain valuable resources, but are difficult to recycle due to their heterogeneity and pollutant load. The “MeteoR” project aims to reintroduce these fine fractions into the material cycle, to advance the circular economy and to reduce CO2 emissions. This project is implemented through a variety of interdisciplinary approaches:
First, the fine fractions are characterized and mechanically processed. This process aims to produce recyclable concentrates, secondary raw materials and pollutant-removed alternative fuels for the cement industry.
Another focus is on testing thermochemical treatment processes suitable for fine fractions that cannot be further mechanically treated.
In parallel, the formation of slags during thermochemical treatment is being researched. These slags could potentially serve as alternative binders, cement admixtures, or concrete admixtures with hydraulic reactivity.
Finally, a comprehensive life cycle assessment of the recycling routes studied is carried out, accompanied by a systemic assessment in the area of waste management. This holistic approach aims to evaluate the sustainability and environmental impact of these recycling efforts.
The project thus follows the holistic approach of optimally recycling all components of the fine fractions and closing material cycles without spreading pollutants. The intended results are proven technology concepts for the treatment of previously non-recyclable fine fractions and a deeper understanding of their composition, recycling potential, mobility of pollutants and their removability and immobilization. The project contributes to the achievement of several UN Sustainable Development Goals and EU Green Deal targets.
IME project management: Joscha Kortmann
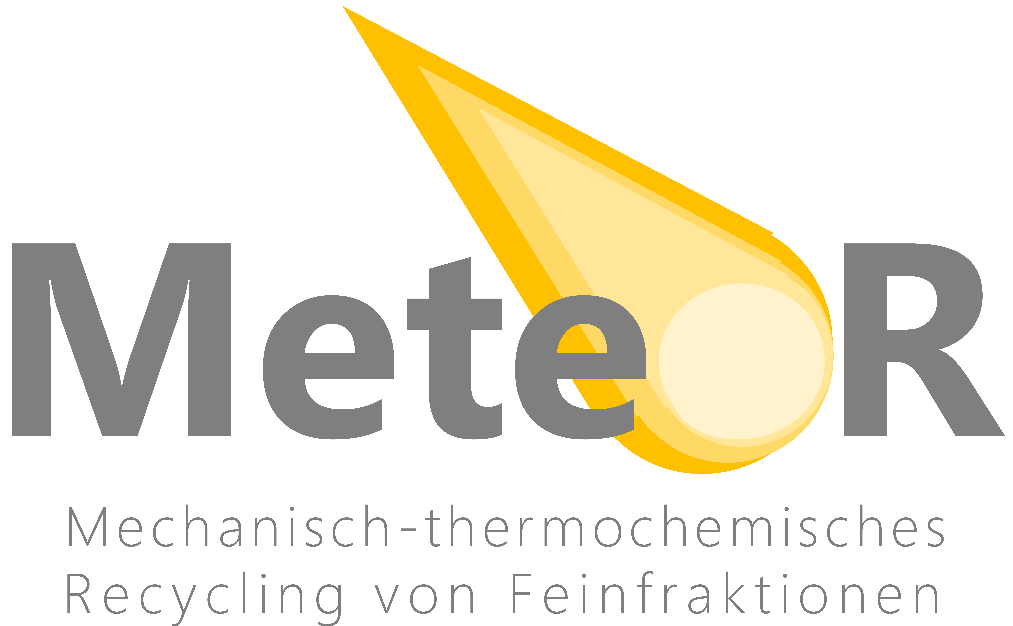
Title
Solar
Type
Grundlagenforschung
Sponsorship
DFG
Duration
01.03.2024 – 01.03.2027
Partner
DLR Köln, Institut für Werkstoff-Forschung
Description
In this research, it is aimed to establish and assess a scientific methodology enabling the targeted synthesis of engineered secondary raw materials from metallurgical residues and recycled fine ceramics as additives. As a use case, fayalitic by-products, commonly used in nonferrous metallurgy, and ceramic processing residues shall be investigated as secondary resources for ceramic particles with specific thermal, optical and structural properties to be used as solar heat transfer and storage medium in concentrated solar power plants (CSP). Ceramic processing residues will be added as dopants to the fayalitic pyrometallurgical by-products to tune the crystallization process and products of smelting process aiming to improve functional properties. Material design and synthesis include adapted doping/smelting/cooling and subsequent heat treatment processes, accompanied by thermochemical modelling. Characterization includes phase- and microstructural evolution as well as thermo-physical properties of derived engineered new ceramics. Properties will be compared with the state-of-the-art ceramic particles prepared from unmodified raw materials in order to validate the new methodology. Thermodynamic modelling and experimental results will be combined to validate this research’s hypotheses and to design a generalized, integrated model workflow to transform metallurgical by-products into value added artificial minerals.
Source of the image: Buck, Reiner; Giuliano, Stefano; Solar tower system temperature range optimization for reduced LCOE; 2019; https://doi.org/10.1063/1.5117522
IME project management: Dorothea Schneider geb. Kenn
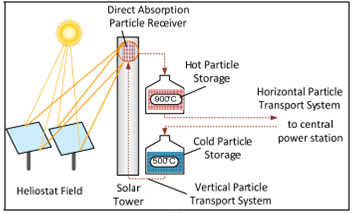
Title
HARARE – Hydrogen as the reducing agent in the recovery of metals and minerals from metallurgical waste
Type
Verbundforschung
Sponsorship
EU – H2020
Duration
01.06.2021 – 31.05.2025
Partner
Sintef – NO, Mytilineos – GR, NTNU – NO, Aurubis AG – DE, RWTH – DE, AdMiRIS – GR, NTUA – GR, RESITEC – NO, KU Leuven – BE, Linde GmbH – DE
Description
Hydrogen as a reducing agent in metallurgy for the recovery of aluminium from red mud in the fixed bed, as well as copper and iron from the smelting phase of primary copper slags.
Title
RECMAG- Sustainable Recovery of Rare Earth Elements (Nd, Dy,Pr) from spent NdFeB magnets
Type
Verbundforschung
Sponsorship
CORNET, ZIM AIF
Duration
01.01.2021 – 31.12.2022
Partner
Istanbul Technical University, Turkei
Description
Nd-Fe-B permanent magnets are a strategic material for a number of emerging technologies. They are a key component in the most energy efficient electric motors and generators, thus, they are vital for energy technologies, industrial applications and automation, and future forms of mobility. Rare earth elements (REEs) such as neodymium (Nd), dysprosium (Dy) and praseodymium (Pr) are found in waste electrical and electronic equipment (WEEE) in volumes that grow with the technological evolution, and are marked as critical elements by the European Commission due to their high economic importance combined with significant supply risks. Since the European Union has been depended on their import, the effective utilization of the available secondary sources (spent NdFeB magnets) is crucial for circular economy and for the sustainable development. Recovery could be an alternative approach to compensate for the lack of rare earths (REs) on the market.
Title
PhöMixBeton – Process for the production of alkali-activated binders by melting mineral residues for an ecologically controlled mix design of concrete
Type
Verbundforschung
Sponsorship
BMBF
Duration
01.02.2022 – 31.01.2026
Partner
Elektrowerk Weisweiler GmbH – DE, TU Berlin Fachbereich Baustoffe und Bauchemie – DE, REMEX Mineralstoff GmbH – DE, BTE Stelcon GmbH – DE, ASCEM B.V. – NL
Description
Use of mineral residue streams as an additive to create a cement binder based on metallurgical slags using the example of EWW/ferrochrome slag.
Cooperation with TU Berlin, as well as EWW, ASCEM Beton, REMEX and BTE Zement to investigate the entire process chain from metallurgical treatment to the finished concrete block.
IME project management: Joao Weiss
Title
Demonstration project for process parameter optimization for the melting of synthetically produced manganese nodules in an electric arc furnace with continuous operation
Type
Verbundforschung
Sponsorship
BMBF
Duration
01.06.2019 – 31.12.2019
Partner
Description
The mining and metallurgical processing of manganese nodules is a chance to recover valuable metals like cobalt, nickel and copper. However, there are also some risks related to the environment. To minimize the impact of a metallurgical process, a multi-step pyrometallurgical process will be investigated in this project, based on a first smelting step to concentrate valuable metals in a metallic phase, while conditioning the slag phase as a substitute for manganese ores. In this project, laboratory trials with synthetic FeNiCuCo alloys and synthetic slags will be carried out to investigate the slagging of valuable metals. After this, a pilot-scale smelting step with synthetic manganese nodules will be carried out to investigate the distribution of those metals in a continuously operated submerged arc furnace.
Title
Development of a energy efficient process through simultaneous melting of SiC-ceramics and WEEE for an optimised recovery of precious metals
Type
Verbundforschung
Sponsorship
VDI/VDE (ZIM-Förderung)
Duration
01.11.2019 – 31.10.2022
Partner
ReMetall AG – Deutschland
Description
Current pyrometallurgical recycling processes have encountered difficulties, as it is not possible to process batches containing more than 5% SiC ceramics – as in soot particle filters. Higher SiC contents would lead to an high viscosity of the melt, resulting in a lack of phase separation between slag and collector metal, making the process uneconomical. The collector metal is utilized to accumulate various precious metals from the ingredient scraps. The primary objective of the project is to increase the proportion of SiC ceramics in the feed mixture for the pyrometallurgical melting process in the electric arc furnace to 30-40%. The feed mixture to be developed will be briquetted for simplified charging and precise composition adjustment. The necessary aggregates must then be supplied with energy to accomplish the precious metal recovery. Through this new process, a considerably more efficient and thus more economical way of recycling soot particle filters will be developed. Treatment techniques will be further expanded and new markets will be opened up.
Title
Slag valorisation for multi metal recovery and mineral resource production
Type
Verbundforschung
Sponsorship
EIT Raw Materials
Duration
01.03.2018 – 28.05.2021
Partner
Baterpol S.A – Poland, BERZELIUS Stolberg GmbH – Germany, IMN Institute of Non-ferrous Metals – Poland, Küttner GmbH & Co. KG – Germany, Vlaamse Instelling voor Technologisch Onderzoek NV (VITO) – Be
Description
Companies operating in recovery of non-ferrous metals generate solid waste in the form of metallurgical slags. Those slags are mostly hazardous for the environment and require storage in landfills. The slag producers bear the costs of building the landfills as well as the environmental fees for the waste storage. The non-ferrous metals producers are looking for an efficient method to treat those slags to reach a “zero-waste” process.
The objective of this project is to upscale a technology to recover metals from slags. These slags are a potential source of base metals. Additionally, after the process the slag can be transformed into a non-hazardous material which can be used in the building sector or for road construction. The processes in this project will be investigated with a submerged arc furnace and a TSL furnace.
Title
CO2MIN – CO2 Capturing through Mineral Raw Materials – Production of Marketable Products with Simultaneous CO2 Sequestration in the Cement Industry
Type
Verbundforschung
Sponsorship
BMBF
Duration
05.2017 – 05.2020
Partner
HeidelbergCement, Institute for Advanced Sustainibility Studies Potsdam, IME-RWTH, AMR-RWTH, GHI-RWTH, LTT-RWTH, AVT-RWTH- Germany.
Description
With the intention of avoiding climate-relevant CO2 emissions, the research project focuses on the development of a process for the mineral sequestration of CO2 using the example of the cement industry. For this purpose, silicate-containing minerals and residual materials are examined for their process suitability and their CO2 binding potential. The carbonate and fine silicate produced in mineral sequestration is an attractive raw material for the cement industry and offers the highest potential for permanent binding of atmospheric CO2. In this project, large-scale industry cooperates with university research to scientifically validate raw material identification, process development including scale-up and product characterization. In order to take a holistic view of the CCU technology, analyses are carried out with regard to the life cycle as well as ecological and social factors.
Title
Optimising the Tantalum Recycling Process through Conditioning of Raw Materials, Process Automation and Material Logistics
Type
Verbundforschung
Sponsorship
EIT Raw Materials
Duration
01.04.2017 – 31.03.2020
Partner
H.C. Starck GmbH – Laufenburg, Institute of Plant Engineering and Fatigue Analysis, Department of Plant Planning and Material Logistics – TU Clausthal, Institute of Mineral and Waste Processing, Waste
Description
In this project, a pyrometallurgical tantalum and niobium recycling process has to be optimized. Aim of the project is to further develop the material pre-treatment, to allow the utilization of tantalum and niobium containing sludge and fines in an electric arc furnace. The implementation of enhanced material logistics is investigated, to decrease the production time in the plant. The automation of process steps in combination with online analytics will enhance the material recovery, the selectivity of the process and to decrease smelting times and therefore the energy consumption in the furnace.
Title
EU Training Network for Resource Recovery through Enhanced Landfill Mining
Type
No information
Sponsorship
EU
Duration
–
Partner
KU Leuven-Belgien, UGent-Belgien, MUL-Österreich, UNIPD-Italien, ETH-Schweiz, LIU-Schweden KTH-Schweden, Shanks SA-Belgien
Description
Europe has somewhere between 150,000 and 500,000 landfill sites, with an estimated 90% of them being “non-sanitary” landfills, predating the EU Landfill Directive of 1999. These older landfills tend to be filled with municipal solid waste and often lack any environmental protection technology. In order to avoid future environmental and health problems, many of these landfills will soon require expensive remediation measures. This situation might appear bleak, but it does present us with an exciting opportunity for a combined resource-recovery and remediation strategy, which will drastically reduce future remediation costs, reclaim valuable land, while at the same time unlocking valuable resources. However, the widespread adoption of Enhanced Landfill Mining (ELFM) in the EU, as envisaged by NEW-MINE, urgently requires skilled scientists, engineers, economists and policy makers who can develop cost-effective, environmentally friendly ELFM practices and regulatory frameworks. All this demands a European commitment to concerted, inter- and transdisciplinary research and innovation. NEW-MINE trains 15 early-stage researchers (ESRs) in all aspects of landfill mining, in terms of both technological innovation and multi-criteria assessments. The technological innovation follows a value-chain approach, from advanced landfill exploration, mechanical processing, plasma/solar/hybrid thermochemical conversion and upcycling, while the multi-criteria assessment methods allow to compare combined resource-recovery/remediation ELFM methods with the “Do-Nothing”, “Classic remediation” and “Classic landfill mining with (co-)incineration” scenarios. By training the ESRs in scientific, technical and soft skills, they become highly sought-after scientists and engineers for the rapidly emerging landfill-mining and broader raw-materials industries of Europe.
Title
European Training Network for Zero-waste Valorisation of Bauxite Residue (Red Mud)
Type
No information
Sponsorship
EU
Duration
01.12.2014 – 31.11.2018
Partner
Katholieke universiteit Leuven, Helsingin Yliopisto, Kungliga Tekniska Högskolan, national Technical University of Athens, Tartu Ulikool, MEAB Chemie Technik GmbH Aluminium of Greece Industrial Commer
Description
To tackle its (critical) raw material dependency, Europe needs comprehensive strategies based on sustainable primary mining, substitution and recycling. Freshly produced flows and stocks of landfilled industrial residues such as mine tailings, non-ferrous slag and bauxite residue (BR) can provide major amounts of critical metals and, concurrently, minerals for low-carbon building materials. The European Training Network for Zero-Waste Valorisation of Bauxite Residue (REDMUD) therefore targets the vast streams of new and stockpiled BR in the EU-28. BR contains several critical metals, is associated with a substantial management cost, whereas spills have led to major environmental incidents, including the Ajka disaster in Hungary. To date, zero-waste valorisation of BR is not occurring yet. The creation of a zero-waste BR valorisation industry in Europe urgently requires skilled scientists and engineers, who can tackle the barriers to develop fully closed-loop environmentally-friendly recovery flow sheets. REDMUD trains 15 researchers in the S/T of bauxite residue valorisation, with emphasis on the recovery of Fe, Al, Ti and rare earths (incl. Sc) while valorising the residuals into building materials. An intersectoral and interdisciplinary collaboration of EU-leading institutes and scientists has been established, which covers the full value chain, from BR to recovered metals and new building materials. Research challenges include the development of efficient extraction of Fe, Al, Ti and rare earths (incl. Sc) from distinct, NORM classified BRs and the preparation of new building materials with higher than usual Fe content. By training the researchers in pyro-, hydro- and ionometallurgy, electrolysis, rare-earth extraction and separation technology, inorganic polymer and cement chemistry, Life Cycle Assessment (LCA), NORM aspects and characterisation, they become the much needed scientists and engineers for the growing European critical raw materials industry.
Title
ResourcesKolleg.NRW Resource extraction from mixed waste fractions
Type
No information
Sponsorship
NRW
Duration
01.01.2013 – 31.12.2016
Partner
Fachhochschule Münster
Description
The technical objective of the research cooperation is the resource-efficient and environmentally sound material and energy recovery of previously insufficiently used waste fractions, the conservation of natural resources and the minimization of waste disposal. Specifically, this objective is to be achieved by recovering and exploiting valuable metals from mixed, composite-rich waste fraction (for example electronic scrap, shredder light fractions, fractions from the building and infrastructure stock etc.) while at the same time using the plastic part of the waste materially and/or energetically. Also, the (metallurgical) use of the coke, which is obtained in the thermochemical treatment of the composite fractions, should be considered.
Title
Loss-minimized metal recycling from waste incinerators by means of sensor-assisted sorting – VeMRec
Type
No information
Sponsorship
BMBF
Duration
01.05.2012 – 30.04.2015
Partner
MAV GmbH, Steinert Elektromagnetbau GmbH, Umicore AG & Co. KG-Belgien, Scholz AG, Werk AluStockach GmbH, pbo Ingenieurgesellschaft mbH, RWTH Aachen University, I.A.R.-DE
Description
The aim of the collaborative project is to optimise the recovery of non-ferrous metals from the anthropogenic raw material source of waste incineration grate ash, taking into account the entire supply chain. This includes the separation of the non-ferrous metals from the grate ash with reference to metallurgical aspects as well as product sales potentials. From the approx. 5 million tonnes of grate ash produced annually, approx. 32,000 tonnes of non-ferrous scrap metal are currently separated, which mainly contains aluminium, copper and zinc, but also precious metals such as silver. Process optimisation measures such as a classification system for specific material groups, which is to be further developed in the joint project and implemented on an industrial scale, will enable this quantity to be increased fourfold to around 130,000 t/a. This means that in the past 10 years in Germany alone, non-ferrous metals worth around €1 billion have been disposed of unused via the raw material source grate ash.
Title
Dismantling and avoidance of red mud dumps
Type
Verbundforschung
Sponsorship
BMBF
Duration
01.05.2012 – 30.04.2016
Partner
Remondis Production GmbH, DK Recycling und Roheisen GmbH, Geocycle c/o Holcim AG-Deuschland
Description
The aim of this research network is the development of an efficient and flexible treatment process for red mud from primary aluminum production, which includes the extraction of high-grade aluminum hydroxide (coupled with the extraction of so-called critical metals, in particular gallium), the thermal production of pig iron, as well as the treatment of the mineral by-product for use in the building materials industry, such as mineral wool production.The innovation of the project is based on the comprehensive optimization of the raw material efficiency of a process combination consisting of a specialized pressure leaching of the residuum, the targeted extraction of critical technology metals and subsequent melting process in an electric furnace as an established, economical process, but with the main objective of driving the slag to mineral and recoverable product.
Title
Electrorefining of slags based on copper
Type
Verbundforschung
Sponsorship
BMBF
Duration
01.03.2009 – 30.08.2010
Partner
Donetsk National Technical University-Ukraine
Description
The purpose of this work is a development electroslag technology of the conversion of copper-containing slag to obtain the charge copper stocking up and utilization of fire refining slags. At electroslag melting (ESR), running under the layer of slag, sharply falls the oxidation of the metal, but if it and occurs, that oxide are assimilated by slag. Besides, row oxide can be restored in the slag bath. Due to this, under ESR simultaneously enlarge the question, both reductions of losses of the metal, and increasing its purity. For treatment of copper containing slag by method of ESR it is practically necessary to organize the process of the simultaneous reduction of copper oxides and melting metallic (copper) component of slag. Reduction of oxides by carbon in slag allows to solve this problem.
Title
Reducing the environmental footprint of primary aluminum production
Type
No information
Sponsorship
EU
Duration
–
Partner
N.T.U.A. Laboratory of Metallurgy, Transition State Industries, Aluminium of Greece Saar Stahl, Deutschen Rockwool, Weizmann Institute of Science, E.T.H. Zurich
Description
Many technological concepts for an alternative aluminium production process have been developed during the last century, because the still utilized Hall-Héroult process is one of the most energy and CO2 intensive industrial processes. However no basic approach was able to prevail in industrial scale. The most promising alternative
process is still the carbothermic reduction of alumina, which has been investigated by several companies and researchers. The greatest challenges are the extensive aluminium volatilization occurring at high reaction temperatures, the complicated back-reaction and carbide formation mechanisms as well as critical reactor design issues.
Title
Extraction of metals and mineral products from landfilled residues of the mining industry in the Mansfeld area
Type
Verbundforschung
Sponsorship
BMBF
Duration
01.10.2009 – 30.09.2012
Partner
CONMET GmbH, Neue Mansfelder Bergwerkschaft GmbH & Co. KG, UVR-FIA GmbH, AMR RWTH Aachen, MLU Halle‐Wittenberg-Deutschland
Description
Investigation of the recoverability of value-containing products, development of extraction and refining processes by means of thermochemical modeling of the process window based on analyzes and subsequent enrichment of rare metals from preconcentrates by hydrometallurgical enrichment ((high pressure) leaching, precipitation, etc).
Title
Prevention of metal losses in metallurgical slags using copper as an example
Type
Verbundforschung
Sponsorship
BMBF
Duration
01.07.2009 – 30.06.2012
Partner
Norddeutsche Affinerie AG-Deutschland, SMS Demag AG-Deutschland, Aurubis AG-Deutschland
Description
Much of the metals produced worldwide are obtained by smelting metallurgy. However, the process efficiency is limited by the concomitant slag phase, since it still contains some of the valuable metals. By targeted separation and enrichment of these elements in usable product phases, the value metal potential can be better utilized. The aim of this project is the development of an efficient and flexible treatment process for primary metal production slags (shown in the example of copper) that maximizes the overall yield of metallic value components (Ni, Co, Mo, Zn, Sn, Sb, Pb and residual Cu) compared to established methods. In this way, economically at least 90% of the metallic recyclables are to be recovered from slags of metal production as raw metal or concentrate.
Title
Laboratory for thermophysical properties Expansion to a precisely adjustable atmosphere and increased precision
Type
No information
Sponsorship
Otto Junker Stiftung
Duration
01.10.2007 – 31.12.2008
Partner
Linn High Therm GmbH-Deutschland, ISEA Institut für Stromrichtertechnik und Elektrische Antriebe RWTH Aachen-Deutschland, MISIS-Russland
Description
Melting and casting processes increasingly require the exact adaptation of plant data to the material to be treated. On the one hand, this includes the metallic target phase,but also desirable or undesirable secondary phases such as slag. Knowledge of the thermophysical properties such as density, surface tension/wetting angle, viscosity or electrical conductivity are indispensable for this. In recent years, the IME Metallurgical Process Technology and Metal Recycling has started to build a corresponding laboratory for the measurement of thermophysical properties. All devices are self-made and operate in air or with protective gas curtains. This state of the art is inadequate and a professional vacuum and protective gas system is now to be set up at the IME, which allows the measurement of the above-mentioned properties in a melt by changing the sensor.
Title
Discard of fine particles
Type
No information
Sponsorship
EMR
Duration
–
Partner
Centre de Recherches Métallurgiques (C.R.M.), Limburgs Universitair Centrum, Hogeschool Zuyd (HSZuyd)
Description
Die EU-Luftqualitätsrichtlinie hat die Anforderungen zur Begrenzung von Staubemissionen (PM10) in Gebieten mit hoher Verkehrs- und Bevölkerungsdichte sowie hoher Industrieaktivität erheblich verschärft. Davon sind neben dem Verkehrssektor vor allem Industriebetriebe betroffen. Mittel- und langfristig müssen die Unternehmen weitere
emissionsmindernde Maßnahmen durchführen, die für eine Reihe von Firmen in der Euregio Maas-Rhein im internationalen Vergleich spürbare Wettbewerbsbeeinträchtigungen mit sich bringen werden. Die Eisen- und
Nichteisenindustrie, Gießereien, Zementwerke, Kraftwerke und Müllverbrennungsanlagen werden in besonderem Maße davon berührt. Um die Produktion und die Arbeitsplätze in den betroffenen Industriezweigen der Euregio dauerhaft zu sichern, ist es notwendig innovative Verfahren zu entwickeln, die zugleich hochwirksam und kostengünstig sind. Darüber benötigen die Unternehmen kompetente Unterstützung von Experten bei der Beurteilung von Handlungsalternativen. Deshalb ist in der Euregio mit einer wachsenden Nachfrage nach kosteneffektiver Staubminderungstechnologie und fundierter Fachberatung zu rechnen. Immer strenger werdende Vorschriften bezüglich des Umweltschutzes erzwingen auch bei KMU und Industrie die aktive, intensive Auseinandersetzung mit dieser Materie, um die Produktion und die Arbeitsplätze in der Euregio zu halten.
Title
Development of an operational Plan for Environmental Protection from Dusts
Type
No information
Sponsorship
EU
Duration
01.09.2006 – 31.08.2008
Partner
National Technicall University of Athens, The Ukrainian Research and Development Institute of Industrial and Sanitary Purification of gases, Moscow State Institute of Steel and Alloys – Technological
Description
Generally, the abatement techniques and dust management technologies used in the production of iron and steel, ferroalloys, aluminium, copper and zinc at the studied plants are in accordance with BATs. Three newer types of ESP with good reported performance could be involved: Moving Electrode Electrostatic Precipitator MEEP, Use of energy pulse superimposition, Electrostatic Space Cleaner Super ESCS. Given that the studied plants are representative of the metallurgical activities in the countries involved in the project (Ukraine, Russia and Kazakhstan), it is evident that in some cases the abatement technique is missing. The formed dust is liberated in at-mosphere. The presence of heavy metals in dust is a high danger for a human health, because of the presence of nanoparticles the health risk is increased. The use of Scanning Mobility Particle Sizer for the measurement of particle size could be offer better picture for formed dust. Small deviations that were noted, concerning the abatement techniques used in the different production stages, should be not viewed as crucial factors of the environ-mental pollution related to the liberation of formed metallurgical dusts.
Title
Integrated Treatment of Industrial Wastes towards Prevention of Regional Water Resources Contamination
Type
No information
Sponsorship
EU
Duration
36 Monate –
Partner
–
Description
The Western Balkan Peninsula is rich in natural resources. Among the most important of them are considered the polymetallic complex sulphide ore deposits used for the production of base (e.g. Cu, Zn, Pb) and precious (e.g. Au, Ag) metals. Exploitation of these ore deposits, one of the most dynamic sectors in the Western Balkan region, along with metal extraction that follows cause severe environmental pollution problems in the area, related to contamination of soil and surface-, groundwater.
This project addresses environmental pollution problems associated with solid and liquid wastes/effluents produced by complex sulphide ore mining and metallurgical activities in two Western Balkan countries, in order to develop preventive and remedial technologies aiming at waste minimization, remediation of waste disposal sites and ultimately prevention of the regional water resources contamination.
In order to achieve this objective, the project deals with (i) harmonization of the environmental legislation in Western Balkan countries through implementation of the relative EU directives and particularly the IPPC directive, (ii) identification and full characterization of the major pollution sources at the selected sites in the two Western Balkan countries and evaluation of the risk for humans and ecosystem on a source-pathway-target principle and (iii) development of an innovative and cost effective integrated management scheme aiming at waste minimization, prevention of surface-, groundwater contamination and safeguarding the ecosystem of the affected areas.
The strategic objective of this project is the reinforcement of environmental protection, one of the three distinct pillars on which sustainable development for both developed and developing countries is based. It is hoped that this will be one of the first steps towards sustainable development of mining and metallurgical industry in Western Balkan countries setting the base for social cohesion, peace, political stability and prosperity on this region.
Title
Development of recycling processes for low-magnesium-containing residuals
Type
No information
Sponsorship
BMBF
Duration
01.03.2005 – 28.02.2006
Partner
Norsk Hydro/Bottrop, Rheinkalk HDW/Herzberg, IFG/Düsseldorf, Foseco/Borken
Description
The joint project currently funded by the BMBF (individual projects with funding codes 01RW0117 and 01RW0302) is developing a process for processing magnesium residues with a low metal content. Initial basic investigations and series of tests with heavily contaminated scrap showed that an industrially produced salt from Rheinkalk HDW already had very good melting properties. There was therefore no need for research into the development of a new smelting salt. Rather, it turned out to be an urgent need for research to minimize the proportion of residual materials to be disposed of in landfills. Since April 2003, test series have been carried out for this purpose, in which industrial salt slags were again used as melting salt at the beginning. Salt enriched with oxides and metallic magnesium could thus be reused up to three times. Further use was not possible due to an increase in viscosity.
Title
Resource-oriented overall consideration of material flows of metallic raw materials
Type
No information
Sponsorship
DFG
Duration
01.01.1997 – 31.12.2005
Partner
IML, I.A.R., LIH, BBK I (heute MRE), AMR, LRST, Bio V, IBH, LFH, BUR RWTH Aachen-Deutschland, STE Forschungszentrum Jülich GmbH-Deutschland, WISO Universität zu Köln-Deutschland
Description
The development of methods for the mapping and analysis of complex material flows of metallic raw materials and the derivation of options for action based on these methods with the aim of a resource-conserving provision and processing of metallic raw materials are the focus of the research work of the SFB 525.