Forschung » Circular Economy for Batteries
The IME represents the field of process metallurgy and metal recycling at RWTH Aachen University. Due to the growing public, political and industrial interest in battery recycling the IME has systematically developed optimal pyrometallurgical and hydrometallurgical recycling concepts for all standard battery systems in cooperation with industrial partners and also in terms of projects funded by the government.
Some of these methods have already been implemented industrially and has been rated as BAT (Best Available Technology).
IME is also developing further efficient recycling concepts for the batteries of the future (Next Generation Batteries).
Energy storage is a key challenge for the global change towards renewable energies. Here, Lithium Ion Batteries (LIB) can be seen as a leading technology. Research at IME in the field of battery recycling also considers the environmental impact of the extraction, treatment and processing of critical raw materials for LIB.
Alumni:
- Dr.-Ing. Lilian Schwich geb. Peters
- M.Sc. Paul Sabarny
- M.Sc. Dominic Dittmer
- M.Sc. Claudia Vonderstein geb. Schier
- M.Sc. Christin Stallmeister
- M.Sc. Wei Song
- Dr.-Ing. Honggang Wang
- Dipl.-Ing. Thomas Träger
- Dr.-Ing. Matthias Vest
- Dr.-Ing. Tim Georgi-Maschler
- Dr.-Ing. Ricardo Sanchez
- Dr.-Ing. Tobias Müller
- M.Sc. Emanuel Sebastian Drude
- M.Sc. Dzeneta Vrucak
- Dr.-Ing. Ksenija Milicevic Neumann

Project List
Title
EarLi: Extraction and purification of lithium hydroxide monohydrate from used electromobile Li-ion batteries for battery cell production
Type
Verbundforschung
Sponsorship
VDIA/DE-IT
Duration
01.04.2023 – 31.03.2026
Partner
ACCUREC-Recycling GmbH – Deutschland; Evonik Operations GmbH – Deutschland; Öko-Institut e.V. – Deutschland;
Description
AThe EarLi project adress the sustainable recycling of lithium from used lithium-ion batteries from the battery cell production funding call. Worldwide, neither industrial or semi-industrial processes nor scientific approaches can be validated that can economically recover this critical raw material in high quality. The loss of value added is increasing dynamically with the rapidly growing amount of waste, and the new European battery legislation will make lithium recovery and recyclate use mandatory from 2026. The project partners are developing and installing an innovative process chain on an industrial scale, in which the lithium in end-of-life battery cells is first transformed into water-soluble lithium compounds using energy-neutral thermolysis. This transformation enables the earliest possible extraction of lithium from the black mass by aqueous neutral leaching, thus preventing dissipative dispersion in the subsequent extractive metallurgical treatment steps of the black mass. A new type of electrolytic membrane filtration then separates the lithium hydroxide monohydrate, which is preferred by precursor manufacturers, from the solution in high quality. The EarLi process chain, which has been tried and tested on lab scale, is particularly characterized by the complete elimination of chemicals, low resource requirements due to the water cycle and low energy consumption due to the energy-neutral thermal pretreatment. This high level of development is the prerequisite for sustainably changing the entire value chain in battery recycling. For the first time, a salable lithium product with a low ecological footprint can be recovered in Europe under competitive cost conditions.
Title
HVBatCycle – HV-battery recycling and resynthesis processes for sustainable and functionally preserved material cycles
Type
Verbundforschung
Sponsorship
Bundesministerium für Wirtschaft und Klimaschutz (BMWK)
Duration
01.01.2022 – 30.06.2025
Partner
Verbundpartner: Volkswagen AG – Deutschland, TANIOBIS GmbH – Deutschland, J. Schmalz GmbH – Deutschland, TU Braunschweig, Battery LabFacto-ry Braunschweig (BLB) mit Instituten IWF- Werkzeugmaschinen und Fertigungstechnik, elenia – Institut für Hochspannungstechnik und Energiesysteme, iPAT – Partikeltechnik, ICTV – Chemische und thermische Verfahrenstechnik, InES – Energie- und Systemverfah-renstechnik – Deutschland, Fraunhofer Institut für Schicht- und Oberflächentechnik (IST) – Deutschland Assoziierte Partner: Open Hybrid LabFactory e.V. – Deutschland, Advanced Measurement Technology, Inc. – Deutschland, Otto Junker GmbH – Deutschland
Description
The project “HVBatCycle” has the overall objective to develop and understand innovative, sustainable and energy-efficient processes along the value chain of high-voltage batteries from electric vehicles in order to enable the closed-loop recycling of battery materials in the near future. In particular, the processes for unmixed dismantling, for ecologically efficient recycling of end-of-life batteries and for the production of new battery materials from the recovered secondary raw materials are to be investigated and their scalability and economic viability demonstrated. Based on various previous projects of the participating partners, new and further developments will be presented, how and with which financial as well as technical effort the requirements of the new EU legislation regarding the material recycling of Li-ion batteries can be achieved and even exceeded by the year 2030. Through an interdisciplinary and highly qualified consortium, innovative processes of an interlinked end-to-end value chain are to be developed, investigated and, with the exception of electrolyte processing, taken from the laboratory to prototype implementation at at least TRL6. In addition, it will be examined whether the secondary materials produced are also suitable for reuse in the battery cell in the sense of multiple recycling. In addition, a battery analysis will be carried out upstream of the recycling process to pre-sort the incoming batteries with regard to possible further use in 2nd life.
IME project management: Dominik Schmitz, M.Sc.
Title
CLIMA – Chemical-free lithium recovery from lithium-ion based spent batteries
Type
Verbundforschung
Sponsorship
EFRE.NRW
Duration
01.01.2022 – 31.12.2022
Partner
Accurec Recycling GmbH – Deutschland
Description
By including lithium in the list of critical raw materials, the European Union is giving the light metal strategic importance in the key technology of electromobility. The metal is exclusively imported and proves the supply risk for the development of European cell production. At the same time, the exponentially increasing quantities of old batteries require innovative process concepts to recover lithium in an energy-efficient way and to provide a partial self-sufficiency for the future mobility turnaround under the highest ecological demands.The project outline presented here addresses both resource and energy efficiency for environmentally friendly mobility with the implementation of a successfully vaild laboratory process for chemical-free lithium salt recovery from lithium-ion-based spent batteries. By applying novel extraction and refining methods, a high-quality lithium salt is to be recycled directly from thermally and mechanically pre-treated used lithium-ion batteries with minimal use of operating materials and made available as a starting product for battery cell production. So far, neither industrial processes nor pilot plants are planned throughout Europe. With the revision of the Battery Directive, however, the recycling of lithium is planned to be obligatory in stages from 2026. The CLIMA project aims to fill this gap by extracting lithium and then purifying it from the material flow of used batteries.
The project is financially supported by the European Union and the State of NRW within the framework of the programme \”InnovationUmweltwirtschaft.NRW\” issued by EFRE.NRW (REACT-EU).
Title
S²taR – Development of All-Solid-State Battery Recycling
Type
Verbundforschung
Sponsorship
BMBF – Bundesministerium für Bildung und Forschung
Duration
01.01.2021 – 31.12.2023
Partner
Fraunhofer-Institut für Schicht- und Oberflächentechnik (IST); Forschungszentrum Jülich – Institut für Energie- und Klimaforschung: Werkstoffsynthese und Herstellungsverfahren (IEK-1); TU Clausthal – Institut für Aufbereitung, Deponietechnik und Geomechanik (IFAT); TU Braunschweig – Institut für Werkzeugmaschinen und Fertigungstechnik (IWF); TU Braunschweig – Institut für Partikeltechnik (iPAT);
Description
In addition to conventional liquid electrolyte-based lithium-ion batteries, all-solid-state batteries (ASSB) based on solid electrolytes with lithium-based or lithium-free anodes will be introduced to the market in the upcoming years. The project S2taR addresses the transfer of the already existing and further developed recycling concepts for conventional LIB to future battery systems in order to evaluate and assess the transferability of the mechanical, thermal, pyrometallurgical, and hydrometallurgical recycling strategies to consider a sustainable design for recycling already during the product development phase of production processes and scalable material developments.
IME project management: Emanuel Sebastian Drude
Title
HydroLIBRec- optimized process chain for hydromechanical Li-ion-battery-recycling
Type
Verbundforschung
Sponsorship
BMBF
Duration
01.01.2021 – 31.12.2023
Partner
Fraunhofer IWKS – Fraunhofer-Einrichtung für Wertstoffkreisläufe und Ressourcenstrategie – Germany, Fraunhofer ISC – Fraunhofer Institut für Silicatforschung – Germany, KIT-MVM – Karlsruher Institut für Technologie Institut für Mechanische Verfahrenstechnik und Mechanik – Germany, HZDR – Helmholtz-Zentrum Dresden-Rossendorf e.V. Helmholtz-Institut Freiberg für Ressourcentechnologie – Germany
Description
The focus of this project is the selective shredding of batteries using electrohydraulic shredding, which is done by the cooperation partner IWKS. The battery cells are thermally pre-treated at the IME and sent to IWKS. After shredding at the IWKS, the active material is sent back to the IME. Here hydrometallurgical processing is followed with the focus on using organic acids. The products are sent to the ISC for resynthesis of lithium half-cells. Digital twins are produced by the HZDR for the work steps of thermal pretreatment and hydrometallurgy and the process is evaluated by the IWKS using a life cycle analysis.
Title
SIMTEGRAL – Integrated multi Scale System Simulation and sustainability assessment of primary and circular raw material supply chains for Li-ion Batteries
Type
Verbundforschung
Sponsorship
BMBF
Duration
01.11.2020 – 31.10.2023
Partner
TU Braunschweig/IWF (D); TU Braunschweig/AIP (D); Helmholtz-Zentrum DR/HIF (D);
Description
The SIMTEGRAL project within the Recycling & Green Battery Cluster is focused on the analysis and sustainable design of complex value chains of raw materials for Li-Ion batteries. Physically based models of the most important processes for primary and secondary raw material production are being developed and experimentally validated. These models provide significantly more detailed process data sets than previously available. All models will be integrated into a superordinate approach for a techno-economic, social and ecological assessment. The aim is to determine reliable key indicators in the context of energy and resource efficiency, quality (raw material purity), economic efficiency (investment and operating costs), social risks and the environmental impact of the battery raw materials. The project contributes significantly to the holistic understanding of the battery life cycle and focuses on raw material recovery.
IME project management: Dominic Dittmer
Title
DiRectION – Data mining in the recycling of lithium-ion battery cells
Type
Verbundforschung
Sponsorship
BMBF
Duration
01.03.2021 – 29.02.2024
Partner
Institut für Werkzeugmaschinen und Fertigungstechnik (IWF-TU Braunschweig), Institut für Partikeltechnik (iPAT-TU Braunschweig), Fraunhofer-Institut für Keramische Technologien und Systeme (IKTS)
Description
So far, sensor and digitization solutions in industrial recycling operations are only available in rudimentary form and only for individual processes. The DiRectION project focuses on the systematic collection and processing of product and process data in battery recycling as well as their cross-process consolidation and evaluation. For this purpose, systems for data acquisition and processing will be installed at existing or future recycling infrastructures of the mechanical, the so-called hydro- as well as pyrometallurgical recycling process chains. The evaluation of the large data volumes is carried out automatically with the aid of data mining, automated data selection or cleaning and evaluation of data records. This will allow to understand the influence of various process parameters on the metal yield or purity of recovered raw materials from the recycling process.
IME project management: Wei Song, Fabian Diaz
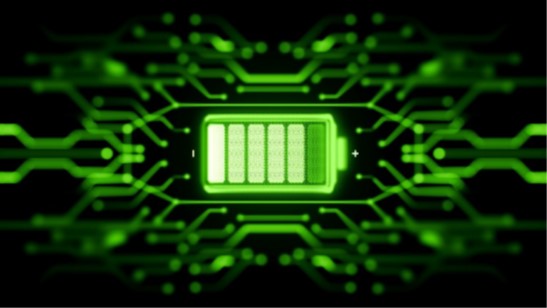
Title
PyroLith – Development of a stable process based on Pyrometallurgy, Slag preparation and Hydrometallurgy for Li recovery from Mn-containing slags
Type
Verbundforschung
Sponsorship
BMBF
Duration
01.12.2020 – 31.11.2023
Partner
TU Clausthal (IEVB), Geozentrum Hannover (BGR), TU Braunschweig (IWF und iPAT) und RWTH Aachen (IMR)
Description
The project aims to explore and develop new routes for efficient recycling of lithium-ion-batteries combining pyrometallurgical, slag preparation and hydrometallurgy. The plan also includes a techno-economic and environmental assessment to determinate the robustness and potential industrial application of the explored processing routs. By pyrometallurgy, several metals existent in batteries such as Co, Ni, Cu, Fe and Mn can be recovered by coagulation into a metallic phase. Nevertheless, the cluster’s ambition is investigating the influence of Al and Mn during the smelting to enhance selective nucleation of LiAlO2 favouring the extraction of lithium by mechanical processing and hydrometallurgy. Besides recovering valuable element, is expected to generate a clean mineral phase to be used as a precursor for the building industry.
Title
ecoLiga – Recycling and resynthesis of carbon materials from lithium batteries: Recovery, processing, reuse and adapted cell design
Type
Verbundforschung
Sponsorship
BMBF
Duration
01.11.2020 – 31.10.2023
Partner
RWTH Aachen / IME- Institut für Metallurgische Prozesstechnik und Metallrecycling | Deutschland HZDR / HIF – Helmholtz-Institut Freiberg für Ressourcentechnologie | Deutschland IWS – Fraunhofer-Institut für Werkstoff- und Strahltechnik | Deutschland TU Braunschweig / IWF – Institut für Werkzeugmaschinen und Fertigungstechnik | Deutschland
Description
The ecoLiga project balances sustainability in terms of manufacturing and recyclability of carbon materials to enable a new and sustainable battery design. Accordingly, a key issue of the project is to close the material cycle of battery components, allowing the use of carbon materials with the background of design for recycling. In this way, the fields of battery manufacturing and recycling can be linked in terms of content and cooperation paths can be identified in order to move in the field of sustainable innovation development. Especially, the developed concepts are validated using lithium-sulfur batteries as an innovative battery system. Thus, an optimal pre-treatment with a suitable extraction process of the active mass, the carbon material recovery, a holistic raw material recovery to maximize the yield, and the resynthesis in the battery system will be carried out.
Title
EARLIMET – Early Stage-Metal Recovery for Energy- and Resource Efficient Recycling of Li-Ion Batteries
Type
Verbundforschung
Sponsorship
BMBF-Kompetenzcluster „Recycling / Grüne Batterie“
Duration
01.10.2020 – 30.09.2023
Partner
1) Fraunhofer-Institut für Keramische Technologien und Systeme (IKTS) Technische Elektrolysen, Tiefe Geothermie und Radionuklidlabor, Deutschland 2) TU Bergakademie Freiberg, Institut für Technische Chemie, Deutschland 3) TU Clausthal, Institut für Nichtmetallische Werkstoffe: Bindemittel und Baustoffe (INW), Deutschland 4) Helmholtz-Zentrum Dresden-Rossendorf (HZDR/HIF), Deutschland
Description
Complete Recycling is a basic prerequisite for closing material usage loop of Li-ion batteries and is thus of increasing importance for the economic efficiency and sustainability of such energy storage systems. Since lithium in particular is largely lost in conventional recycling processes, it should be recovered from the so-called black mass right at the beginning of the process chain. Otherwise a dissipation of Li via various material streams of the overall process can not be avoided. In the research project \”EarLiMet\”, therefore, a comprehensively resource-efficient, predominantly hydrometallurgical recycling of the valuable components in Li-ion batteries up to the TRL 5/6 level is to be developed. The concept pursued in EarLiMet aims at a zero-waste approach, which requires a complete consideration and balancing of the entire process.
IME project management: Daniel Munchen, Ksenija Milicevic Neumann
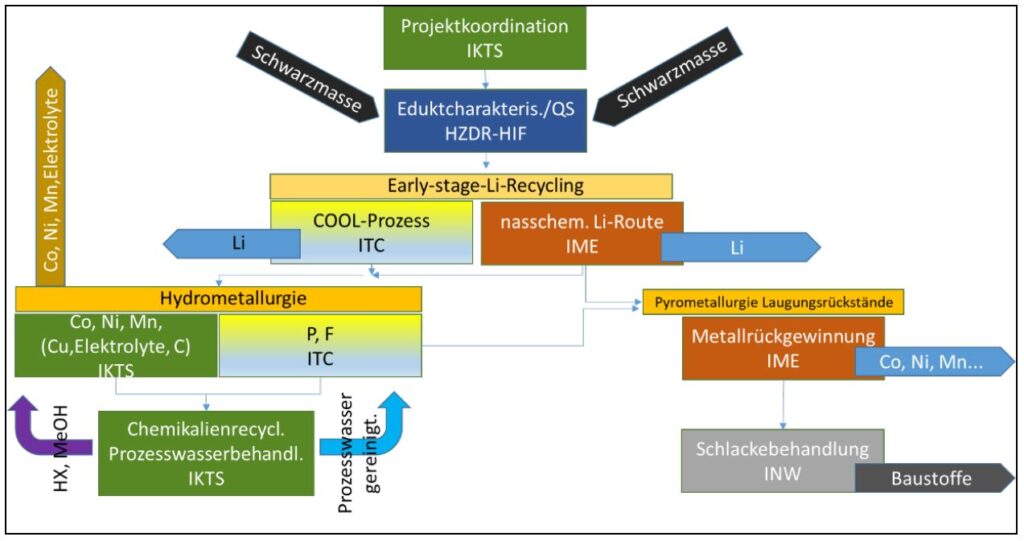
Title
AURRELIA – Optimization of wet processing techniques for the recovery of recyclable fractions from spent lithium-ion batteries
Type
Verbundforschung
Sponsorship
Bundesministeriums für Bildung und Forschung (BMBF)
Duration
01.01.2021 – 30.06.2024
Partner
Lehrstuhl für Fluidverfahrenstechnik (AVT.FVT) – Deutschland Lehrstuhl für Chemische Verfahrenstechnik (AVT.CVT) – Deutschland Institut für Infrastruktur ∙ Wasser ∙Ressourcen ∙ Umwelt (IWARU) – Deutschland
Description
The aim of the AURRELIA research project is to optimize the recycling process of post-consumer lithium-ion batteries (LIBs) by developing suitable processes along the process chain from mechanical to hydrometallurgical processing. The aim is to make the largest possible proportion of a LIB accessible for recycling.
In terms of a zero-waste process, the project aims at high yields and purities of the obtained products. A central part of the project is the material-specific and economical processing of the LIBs, for which suitable shredding and processing methods are examined. Using an optimized shredding technology, the LIBs are comminuted in a wet environment and then separated into solid and liquid phases. This allows for material-specific treatment of the material streams and, thus, a comprehensive recovery of the LIB components is possible. In particular, the focus is on avoiding lithium losses. The process starts with a shredding step in aqueous environment, which eliminates the need to manually dismantle the batteries. This is followed by a product-oriented separation in order to obtain solids and liquid phases as separate fractions. The constituents of the electrolyte and the conducting salt brought into solution are to be selectively separated from the aqueous phase and recovered by means of membrane technologies and precipitation. In the hydrometallurgical processing steps, the wet-chemical process route is to be optimized with regard to the achievable product yield and purity of the metal salts. For the first time, particularly environmentally friendly and biodegradable leaching agents are used. With the results obtained, a concept for optimal LIB recycling is then developed, which is to be tested on pilot scale. The project aims to make a significant contribution to the focus of future LIB recycling processes.
IME project management: Dominik Schmitz
Title
Preliminary study – Development of a basic concept for a \”Circular Value Creation\” project center in Ibbenbüren
Type
Verbundforschung
Sponsorship
Ministerium für Kultur und Wissenschaft des Landes Nordrhein-Westfalen (MKW)
Duration
01.06.2020 – 30.11.2020
Partner
RWTH/ IME Institut für Metallurgische Prozesstechnik und Metallrecycling – Deutschland; RWTH/ CON Lehrstuhl für Controlling – Deutschland; FH Münster/ IWARU Institut für Infrastruktur, Wasser, Ressourcen und Umwelt – Deutschland
Description
With the finalization of the preliminary study \”Project Center for Circular Value Creation\”, a sustainable concept for a \”Battery Recycling Demonstration Center\” in North Rhine-Westphalia has been developed; the center shows numerous unique selling points in Germany due to its scale (demonstration and upscale research) and the comprehensive equipment for closing the loop of used batteries:
Accompanying the project \”Research Manufacturing Battery Cell (FFB)\” in Münster, the possibility of creating a demonstration center for circular value creation from batteries that is visible beyond the state borders was investigated in the present project. The technical demand for this arises from the ensuring of sustainable e-mobility through the most comprehensive circular economy for the total material flow of batteries. From a spatial point of view, Ibbenbüren offers the best conditions for this, since the complete \”battery recycling\” value chain within North Rhine-Westphalia can be developed and realized at this location.
In this preliminary study, a viable concept for a battery recycling demonstration center is presented, which in the future will also take into account the cells newly developed at the FFB. Complex flowcharts have been developed covering the complete battery recycling chain – from screening, disassembly and mechanical processing to material conditioning and metal recovery by pyro- and hydrometallurgical processes. The investments and costs required for realization (construction and operation) have been estimated on the basis of extensive research and indicative price quotations. First financing models have been established. In addition, the first possible partners and interested parties from the fields of plant engineering, OEMs and recycling companies have been identified and compiled in a list. Reliable (verbal) expressions of interest are already available.
IME project management: Elinor Rombach
Title
greenBattUse – Support project Battery life cycle
Type
Verbundforschung
Sponsorship
BMBF – Bundesministerium für Bildung und Forschung
Duration
01.09.2020 – 29.02.2024
Partner
TU-Braunschweig/IWF (D); Fraunhofer/IKTS (D); RWTH/ISEA (D); TU München/EES (D); Fraunhofer/ISIT (D); TU-Braunschweig/AIP (D); Öko-Institut (D)
Description
The GreenBattUse project supports the individual projects of the cross-sectional initiative Battery Life Cycle in the Battery Use Concepts and Recycling & Green Battery clusters. It takes over the central management through coordination, progress monitoring, communication and event organisation. In addition, results are bundled in a central data/document sharing platform. References and standards for the cluster projects are defined to create a basis for assessment. Furthermore, the holistic assessment of different second-use/recycling options for batteries is carried out with regard to the economic, technological and ecological impacts from a life cycle perspective. Based on the outcomes of the cluster projects, recommendations for action are derived for various actors from the fields of politics, business and research. The IME’s scientific contribution focuses on the interface between pre-processing and pyrometallurgy.
IME project management: Elinor Rombach
Title
ProLiMo – Process development for lithium recovery from Li-ion batteries for tomorrow\’s raw material security
Type
Verbundforschung
Sponsorship
DBU – Deutsche Bundesstiftung Umwelt
Duration
01.11.2021 – 30.04.2023
Partner
K-UTEC AG Salt Technologies – Deutschland
Description
The replacement of energy sources of fossil origin by CO2-neutral resources entails major changes in numerous areas of life and society. In particular, the energy supply itself, industry, transport and private households are affected. Consequently, electrochemical energy storage for stationary applications as well as in vehicles by means of accumulators will gain rapidly increasing importance in addition to already established areas of application. Li-ion accumulators (Li-ion batteries) are currently, as well as in the future, the most promising battery types for these applications and consequently lead to an increasing demand for raw materials for the production of these batteries. The recycling of the resulting battery waste is essential, due to the unique selling proposition as a rechargeable energy storage system, in order to ensure raw materials and resource independence. The steadily increasing production of Li-ion batteries can lead to a shortage of critical raw materials such as cobalt and lithium on the global market. The recovery of secondary raw materials from used Li-ion batteries through recycling is therefore becoming increasingly important. However, common to all research activities as well as industrial processes is that lithium, as a base element, cannot be recovered at all or only insufficiently in the recycling processes, and the recovery of the graphite contained in batteries also poses challenges to industry and research facilities. This research project aims to close this knowledge gap and to make a significant contribution to a zero-waste recycling concept for Li-ion batteries by recovering lithium and graphite based on and optimising existing processes.
Title
Central project – Slag synthesis, design and characterization
Type
Verbundforschung
Sponsorship
DFG
Duration
01.10.2021 – 01.10.2027
Partner
MVTAT TU Freiberg – DE
Description
The project works on a combination of metallurgical slag generation and mechanical slag formulation as well as corresponding characterization. The service character of the project towards the PP derives from the supply of defined formulated and characterized slag samples for further projects, since it is necessary to provide sufficient quantities of EnAM containing slags already in the early stage of the first funding period to make the PP operative. The EnAM system chosen is LiAlO2 n*SiO2, which typically occurs in a Al-Ca-Mg slag system during metallurgical Li-ion-battery recycling. The service comprises a reproducible synthesis of the slag containing EnAM grains with a given composition as well as defined grain size. Furthermore, the solidified slag has to be tailored concerning particle size range and the particle size distribution prior to the supplying it within the PP. Additionally, it is necessary to provide fundamental information on the concentration and size (distribution) of the Li-EnAM-grains. This is all the service task of this central project. The research part of the central project focuses on two areas: metallurgical-engineering investigations and quantification of the metallurgical processing properties of Li-EnAM-system complementary to the service-synthesis and the ongoing development of 3D-geometallurgical characterization methods and their application to create a deep insight in the structure and the composition of the heterogeneous material structure of the Li-EnAM system. The fundamental engineering-metallurgical challenge aims at the influence of the processing and cooling parameters on the properties of the Li-EnAM, e.g. grain-size, grain-shape, yield, concentration or mechanical stability. The characterizing part aims at the development of a holistic characterization method for the EnAM, to quantify the 3D-structure, elemental and mineralogical composition of the solidified slag using 3D X-ray tomography. This will help to understand the distributed nature of volumetric crystallization und segregation effects. The image analysis of the tomograms is developed to deduct different particle and or grain related geometrical size and shape parameters. One further focus will be put on the determination of the 3D-intergrowth within the EnAM, e.g. the phase boundaries between individual grains.
IME project management: Joao Weiss
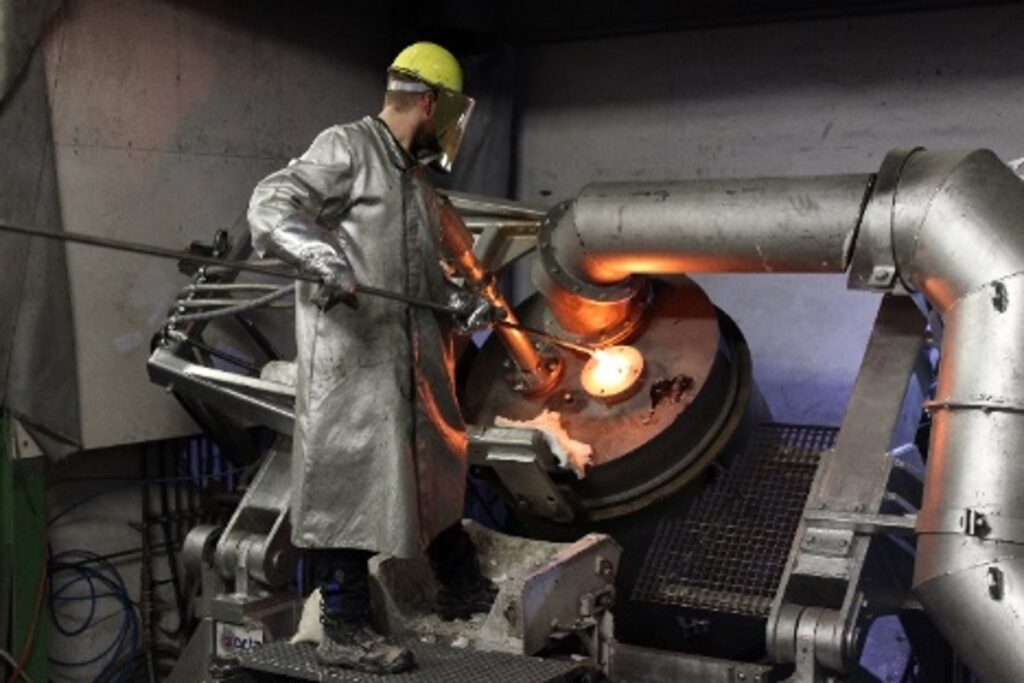
Title
InnoRec – Innovative Recyclingprocesses for new Lithium-Cellgenerations
Type
Verbundforschung
Sponsorship
BMBF
Duration
01.10.2019 – 30.09.2022
Partner
Technische Universität Clausthal, Deutschland; Technische Universität Braunschweig, Deutschland; TU Bergakademie Freiberg, Deutschland; Westfälische Wilhelms-Universität Münster, Deutschland
Description
The development of new battery systems brings additional, previously unused elements such as silicon, lanthanum or zircon into the battery cells. Since recycling is indispensable for ensuring the supply of raw materials, the objective of the InnoRec project is to develop the best possible recycling methods. A future recycling process must be highly flexible and able to react dynamically to new production techniques and materials. Future processes must, however, also replace the energy-intensive processes currently used for classical LIB with low-energy, environmentally friendly process steps. Mechanical, thermal and chemical process stages must be used and interconnected in different ways for this purpose. The task of the IME is the conception and experimental investigation of the pyrometallurgical recycling pathways, including pyrolysis, erarly-stage Li reovery, melting and solidification.
IME project management: Christin Stallmeister
Title
Libero – Near zero waste Hydrometallurgy for spent Li-Ion batteries- multi element recovery for maximized recycling efficiency
Type
Verbundforschung
Sponsorship
AiF-ZIM
Duration
01.09.2019 – 31.08.2021
Partner
MEAB Metallextraktion AB-Schweden, ACCUREC Recycling-Deutschland, Chalmers University of Technology, Industrial Materials Recycling and Nuclear Chemistry, Schweden
Description
Libero represents a robust and flexible near zero-waste process which is carried out to recover all valuable metals and graphite contained in spent Li-ion batteries (LIBs) for future industrial implementation. This project distinguishes from all given industrial processes by selectively and efficiently recovering the entire range of contained metals by using mechanical treatment and hydrometallurgical processes to achieve higher product revenues than expected process costs.
Title
Si-Drive – Silicon Alloying Anodes for High Energy Density Batteries comprising Lithium Rich Cathodes and Safe Ionic Liquid based Electrolytes for Enhanced High VoltagE Performance
Type
Verbundforschung
Sponsorship
European Union’s Horizon 2020 research and innovation programme
Duration
01.01.2019 – 31.12.2023
Partner
University of Limerick (IE), Karlsruhe Institute of Technology (DE), Meyer Burger B.V. (NL) Italian National Agency for New Technologies, Energy and Sustainable Economic Development (IT) Solvionic (FR
Description
Si-DRIVE will develop the next generation of rechargeable Li-ion batteries, allowing for cost competitive mass market EVs by transformative materials and cell chemistry innovations, delivering enhanced safety with superior energy density, cycle life and fast charging capability using sustainable and recyclable components. The technology encompasses amorphous Si coated onto a conductive Cu-silicide network as the anode with polymer/ionic liquid electrolytes and Li-rich high voltage (Co-free) cathodes via processes that are scalable and demonstrably manufacturable within Europe. The technology will also demonstrate suitability for 2nd life applications at reduced energy density beyond the primary EV lifetime, prior to cost effective materials recycling, consistent with a circular economy. The consortium boasts the required partner expertise to deliver this technology and spans material design and synthesis, electrochemical testing, prototype formation, life cycle assessment and recycling
Title
MERCATOR – Material Efficient Recycling for the Circular Economy of Automobile Storage by no Waste Technology
Type
Verbundforschung
Sponsorship
BMU
Duration
01.08.2019 – 31.07.2022
Partner
ACCUREC Recycling GmbH – Deutschland, CTG GmbH – Deutschland, UVR-FIA GmbH – Deutschland, Öko-Institute e.V. – Deutschland, Ford AG – Deutschland SQM S.A. – Belgien
Description
The aim of the MERCATOR project is the optimization of the Li-Ion battery recycling process against the background of ecological, economic and supply aspects. The focus is on the recovery of all valuable secondary materials, some of which have been classified as critical, while improving the ecobalance of these batteries. Therefore an innovative pilot-scale zone furnace is beeing developed in which vehicle batteries are thermally deactivated and pre-treated for a subsequent, material-efficient treatment process. Materials, such als lithium, that were previously not recyclable are to be recovered at an early stage of the process by means of phase transformation with low losses. In parallel, it is intended to reduce the contained oxides to elemental metals and to remove them prematurely so that the subsequent hydrometallurgical process is relieved. In addition, the preparation of the contained graphite is investigated in order to make it available again as raw material.
IME project management: Christin Stallmeister
Title
Batteries2020: Towards realistic European Competitive Automotive Batteries
Type
No information
Sponsorship
EU
Duration
01.09.2013 – 31.08.2016
Partner
Ikerlan S.Coop.-Spanien,Umicore NV,Vrije Universteit Brüssel,Kellen Europe S.A.-Belgien,Abengoa Research SL-Spanien,Leclanche Sa-Schweiz,Centro Ricerche Fiat SCPA-Italien,Aalbrog Universitet-Dänemark
Description
A lifetime of 4000 cycles at 80 % DOD and an energy density of 250 Wh/kg is a target for automotive batteries. The Batteries2020 project takes several steps to increase lifetime and energy density of large format lithium ion batteries towards these goals. Our approach is based on three parallel strategies: 1) highly focused materials development; 2) understanding ageing and degradation phenomena; and, 3) routes to reduce battery cost. We will improve cathode materials based on nickel/manganese/cobalt (NMC) oxides. Such materials have a high chance to be up-scaled and commercialized near-term. Only then, cell development efforts can be translated from pilot to mass production, a prerequisite for qualification in the automotive industry. We will start with state of the art cells and will develop two improved generations of NMC materials and cells towards high performance, high stability and cycleability.
Title
Demonstration plant for a cost-neutral, resource-efficient processing of disused Li-Ion batteries of electromobility
Type
No information
Sponsorship
BMU
Duration
01.04.2012 – 30.09.2015
Partner
ACCUREC GmbH-Deutschland
Description
Among other things, the electromobility government program will be used to implement concepts with integrated demonstration plants to increase economic acceptance and competitiveness through cost reduction. Part of this includes the previously high disposal costs of the battery modules, which must already be taken into account in today’s electric vehicles in line with the extended product responsibility of automobile manufacturers. For the first time, the development and pilot project is intended to combine low-cost processing with maximized recovery of valuable battery components, in contrast to recycling methods currently available industrially and currently under development.
Title
EcoBatRec- Demonstration system for cost-neutral, resource-efficient processing of spent Li-ion batteries from electromobility
Type
Verbundforschung
Sponsorship
BMUB
Duration
01.04.2012 – 31.03.2016
Partner
ACCUREC Recycling GmbH, Mülheim-DE, IME-RWTH University, Aachen-DE
Description
The main objective of the EcoBatRec joint project was to develop and test economically viable recycling technologies for lithium-ion batteries from electric vehicles. A new process step, autothermal vacuum pyrolysis, enables new process sequences in the area of crushing, classification and sorting and separation of the different material fractions. For the recovery of lithium, two alternative processes, drag-gas evaporation and vacuum evaporation, were investigated. The findings are being used in a demonstration plant operated by Accurec Recycling GmbH.
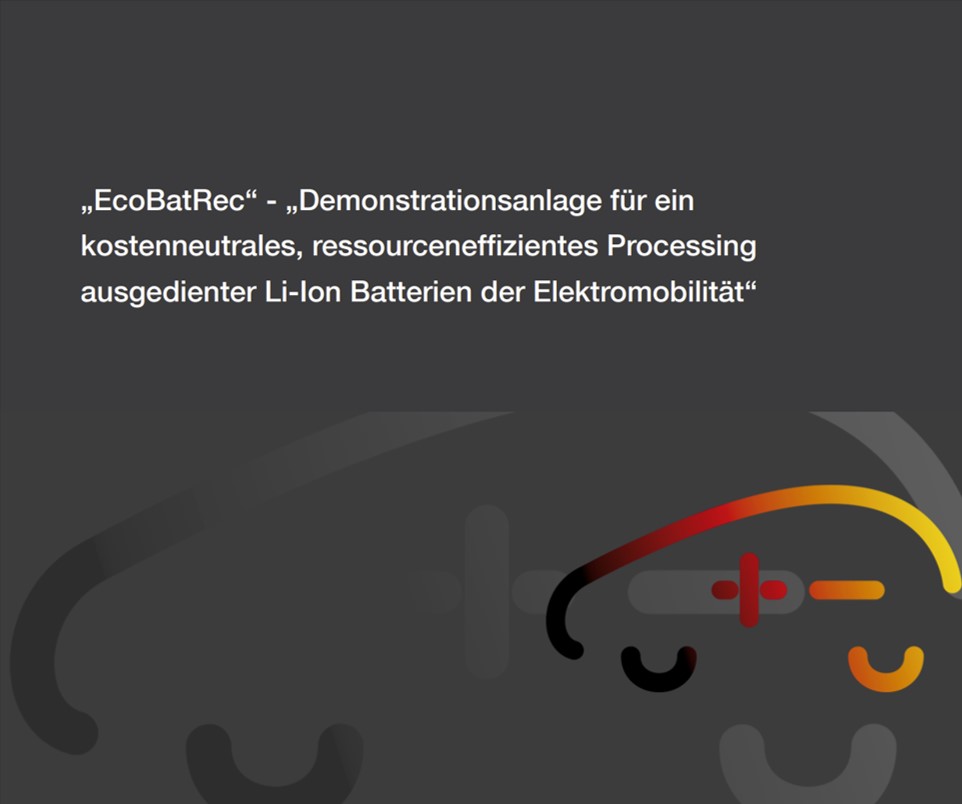
Title
Recycling process for spent nickel metal hydride batteries from future hybrid vehicles and consumer applications
Type
No information
Sponsorship
Landesamt für Natur-, Umwelt- und Verbraucherschutz Nordrheinwestfalen
Duration
01.02.2009 – 30.07.2012
Partner
ACCUREC Recycling GmbH-Deutschland
Description
The state of the art in recycling small nickel metal hydride batteries (NiMH) is their use as an inexpensive source of nickel in steel production. Energy-intensive metal contents are either not used (cobalt) or diluted in a slag (rare earths).
IME project management: Elinor Rombach
Title
Sustainable mobility concepts based on electromobility and urban infrastructure
Type
No information
Sponsorship
Bundesministerium für Verkehr, Bau und Stadtentwicklung
Duration
01.10.2009 – 31.08.2011
Partner
STAWAG, Stadt Aachen, IFHT, ISEA, IAEW, ISB, WZL, DB Fuhrpark, EcoCraft Automotive GmbH & Co. KG, FKA mbH, Hans Hess Autoteile GmbH, HOPPECKE Batterien GmbH & Co. KG, InnoZ GmbH
Description
Within the framework of “E-Aix: Elektromobiles Aachen”, commercial vehicles, electric scooters and pedelecs are partly purchased directly or their purchase promoted. In the field of energy storage for these vehicles, several competing technologies are currently available on the market. They differ mainly in terms of manufacturing costs, service life, weight and energy density. The aim of this study is to show which changes will occur for vehicle battery distributors, workshops, collection points, recycling companies and the city of Aachen as a result of a change in technology towards electromobility from the point of view of the End of Life problem. Not only recycling concepts will be presented, but also secondary use concepts and their advantages and disadvantages.
Title
Technical Feasibility and Legal Frame of Spent-Portable-Battery-Recycling in Mexico
Type
No information
Sponsorship
BMBF
Duration
01.07.2009 – 31.06.2012
Partner
IPN National Polytechnic Institute Mexico City, IPN National Polytechnic Institute Mexico City-Mexiko
Description
An increasing amount of attention has recently been given to developing environmentally clean technologies for the recycling of spent portable batteries in the world, taking two main aspects into account, the possibility of their use as raw material in a time where their components became limited and expensive and their possible environmental harmful effect if they are not disposed in a correct way. Mexico, as one of the highest populated countries has suffered an enormous increasing in consume of technological dispositives with portable batteries in the last years, like computer, CD-player, Walk-man, cellular phone, and so on, but there is not a parallel development of collection strategies of the batteries and actual regulation laws.
Title
Technical Feasibility and Legal Frame of Spent-Portable-Battery-Recycling in Mexico
Type
No information
Sponsorship
BMBF
Duration
01.07.2009 – 31.06.2012
Partner
IPN National Polytechnic Institute Mexico City, IPN National Polytechnic Institute Mexico City-Mexiko
Description
An increasing amount of attention has recently been given to developing environmentally clean technologies for the recycling of spent portable batteries in the world, taking two main aspects into account, the possibility of their use as raw material in a time where their components became limited and expensive and their possible environmental harmful effect if they are not disposed in a correct way. Mexico, as one of the highest populated countries has suffered an enormous increasing in consume of technological dispositives with portable batteries in the last years, like computer, CD-player, Walk-man, cellular phone, and so on, but there is not a parallel development of collection strategies of the batteries and actual regulation laws.
Title
Recovery of recyclables from future Li-ion based automotive batteries
Type
Verbundforschung
Sponsorship
BMBF
Duration
01.02.2009 – 31.07.2012
Partner
ACCUREC Recycling GmbH-Deutschland
Description
For the first time, automotive Li-ion-based battery systems, thanks to their high unit weights and clear identification based on their origin and content, enable the production of uniform input materials in the recycling process. As a result, starting materials of the same composition can be put together and treated batchwise. Due to this circumstance, the extraction of the high-quality organic components and the lithium metal has a new significance. Due to the worldwide resources and the availability of lithium, its recovery is of particular importance within the research project.
The aim is to demonstrate the technical feasibility on a semi-technical scale and to provide the data for an economic and ecological evaluation of the process for expected applications in practice.
Title
HELIOS – High Energy Lithium-Ion Storage Solutions
Type
No information
Sponsorship
EU
Duration
01.11.2009 – 30.04.2011
Partner
Renault-Frankreich
Description
This is a 3 year project to carry out a comparative assessment of 4 various types of High energy lithium-ion battery technology for application in traction batteries for the automotive sector (fully electric vehicles, or for ‘plug-in’ hybrid electric) and for Heavy Duty Hybrid Truck (auxiliary Power Unit). The technology is not yet sufficiently mature to indicate the most appropriate type of cell for any particular application, the work therefore delivers the comparative data covering performance, life, cost, recycling and safety/abuse characteristics to system and vehicle designers and also investors. The above battery performance characteristics are the key issues for the commercialisation of electric and hybrid electric vehicles for high energy applications, requiring a large amount of energy stored on board. The lack of long-term visibility on these issues is limiting the commercial availability of Electric Vehicles and Plug-in HEV.
Title
Process development for the recycling of zinc-carbon / alkaline-manganese batteries with optimized recycling efficiency
Type
No information
Sponsorship
Deutsche Bundesstiftung Umwelt
Duration
01.10.06 – 30.06.07
Partner
REDUX GmbH, Dietzenbach
Description
The aim of the project is to develop an innovative recycling process for spent batteries with a high volume and pollutant potential, which also ensures that the European legal requirements on “Recycling Efficiency” expected this year are met. Contrary to the currently prevailing reprocessing practice of either largely slagging (Mn) or recycling (Mn, Zn, Fe) the metal content of spent batteries by means of mostly multi-stage processes with insufficient metal yields (Mn, Zn, Fe), the new low-emission ELBO process to be developed here will also be used to:
– return important non-ferrous metals such as Mn, Zn and Fe to the raw material cycle to a much greater extent (optimisation of Mn output),
– improve Product qualities (production of marketable metal products),
– reduce Energy consumption figures of the process chain significantly (process chain shortening and C-utilization) and
– reduce Process and transport-related emissions significantly (process chain shortening and low-emission electric furnace technology).
IME project management: Elinor Rombach
Title
\”LiVe\” lithium battery composite structures
Type
No information
Sponsorship
BMBF
Duration
4 Jahre
Partner
TU Braunschweig, Universität Duisburg-Essen, Universität Erlangen, Leibniz-Universität Hannover, Justus-Liebig-Universität Gießen, Westf. Wilhelms-Univ. Münster
Description
Ziel und Vision des Projektes ist die deutliche Performance-Steigerung von zukünftiger Lithium-Hochleistungsbatterien durch die Entwicklung von Komposit-Elektrodenschichten mit maßgeschneiderter Strukturierung bis in den Mikro- und Nanobereich. Die Aufgabe schließt den gezielten Aufbau der Separator-/Elektrolytschichten und der Elektrolyt/Elektrode-Grenzflächen sowie die Prozesstechnik, die die Voraussetzung für eine reproduzierbare Komponentenfertigung ist. Die erwartete Performancesteigerung bezieht sich gleichermaßen auf Leistungs- und Energiedichte, die Kapazität sowie auf die Zyklenstabilität und kalendarische Lebensdauer der Akkumulatoren.
Title
Recovery of raw materials from Li-Ion accumulators
Type
No information
Sponsorship
BMBF
Duration
01.07.2004 – 30.06.2007
Partner
Accurec GmbH, UVR FIA GmbH-Deutschland
Description
The aim is to develop a recycling process that minimises the amount of residual material and has few process stages, which converts the metallic valuable components (Co, Cu, Al, Fe, Li) and the high-quality conducting salt LiPF6 from the Li-Ion batteries into such a form that they can be reused in the battery production process. The aim is also to prove the technical feasibility on a semi-technical scale and to provide the data for an economic and ecological evaluation of the process for applications to be expected in practice. By combining mechanical processes and vacuum-thermal treatment methods, complex hydrometallurgical process steps are to be avoided. Among the innovative core processes of the process concept are the quasi-isothermal vacuum distillation of the electrolyte temperature-sensitive conductive salt with simultaneous deactivation of the Li-Ion cell, the comminution of the batteries and subsequent sorting into a carbon-containing Co-Li concentrate as well as concentrates of copper and aluminium. The Co-Li concentrate contains the conductive salt which is then washed out with the recovered electrolyte for filtering and reuse. By reducing the melting down of the Co-Li concentrate, Co is obtained as a metal as well as a Li-containing slag concentrate. Conversion to Li chloride and subsequent fused-salt electrolysis enables the production of metallic lithium. With this holistic approach, the value-intensive ingredients can be recovered as marketable recycling products.
Title
Recovery of valuable metals nickel, cobalt and rare earth from nickel-metal hydride battery scrap for reuse in battery alloys
Type
No information
Sponsorship
BMBF
Duration
01.01.2002 – 31.12.2004
Partner
UVR-FIA GmbH, ACCUREC GmbH-Deutschland
Description
Development of a low-waste recycling process for spent Ni-MH batteries from the consumer sectors of communication, video/audio and computers for the recovery of valuable metals, in particular nickel, cobalt and rare earth metals, and extensive recycling of other battery components.
The results of the research and development work will be made available to the industry, in particular to battery manufacturers, following the positive course of the project, in order, on the one hand, to meet the requirements of the legislator with regard to battery recycling (Battery Ordinance of April 1998) and, on the other hand, to sustainably improve the competitive situation of German alloy manufacturers in comparison to foreign competitors.