Ausrüstung » Prozessmetallurgie
35l kippbarer Widerstandsofen
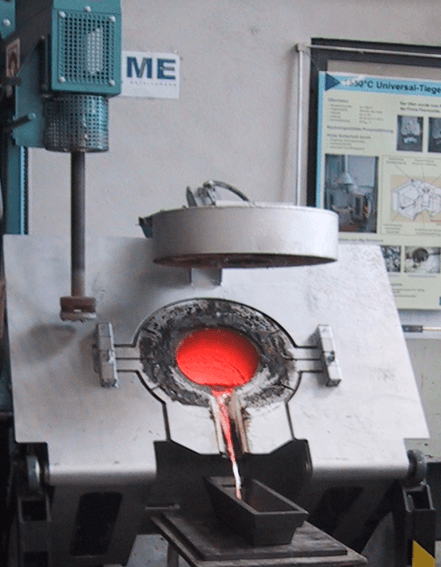
Application area:
- sicherheitstechnisch speziell für Magnesiumschmelzen ausgelegt (Fe-Tiegel)
- Schmelzen von Al, Cu, Pb, Zn in Fe oder Graphit Tiegel
- Schmelzbadbehandlung möglich mit installiertem, industriellen, vollautomatischem Foseco Rühr- und Entgasungsgerät
Performance data
- Der mit SiC Stäben widerstandsbeheizte Ofen
- Volume: 35 l
- Feinmotorischer, hydraulischer Kippantrieb erlaubt ein kontrolliertes Dosieren während des Abgusses (ferngesteuert)
- Hydraulischer Deckel (ferngesteuert) mit Schutzgas-Ringleitung
- Die Heizleistung des Ofens beträgt 46 kW
- Temperatur im Ofen kann gradgenau eingestellt werden
- Notauslauf im Boden zur gezielten Schmelzabfuhr bei Tiegelbruch
Contact person
M.Sc. Dorothea Schneider geb. Kenn
DC-Lichtbogenofen (GLBO)
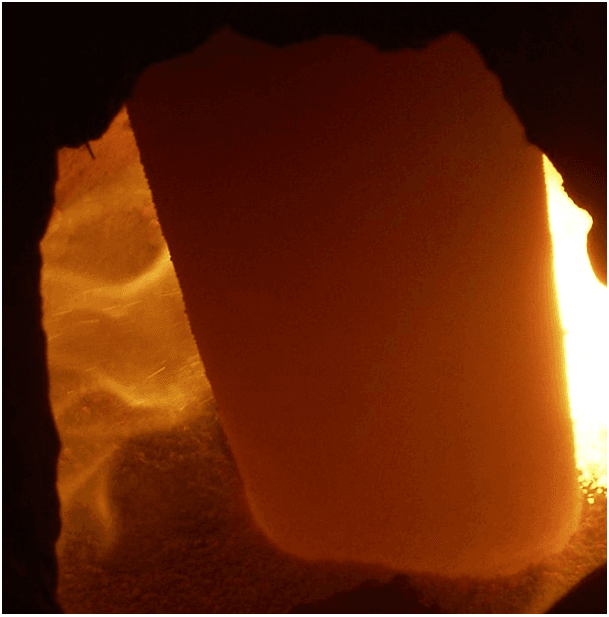
Application area:
- Carbothermische Herstellung von Silizium / Aluminium
- Batterierecycling
- Schlackenmetallurgie
- Stahlmetallurgie
- Kupfermetallurgie
Performance data
- Gleichstrombetrieb
- Trafo Anschlussleistung 700 kVA
- Herddurchmesser 0,95 m
- Gefäßhöhe 1,45 m
- Messtechnik zur Erstellung einer Energiebilanz
Contact person
Dipl. -Ing. Joao Weiss
DC-Lichtbogenöfen (KLBO & MLBO)

Application area:
- Recycling von AlMn, ZnC oder Lithium-Ionen Batterien
- Recycling von Schlacken
- Reduktion oxidischer Komponenten
- Herstellung von AlSi-Vorlegierungen und Silizium
- Herstellung von Ferrolegierungen und Nichteisenlegierung
- Verwertung von Reststoffen
Performance data
- Kleiner Lichtbogenofen (KLBO) = 1,5 l Schmelzvolumen
- Mittelgroßer Lichtbogenofen (MLBO) = 4,5 l bzw. 12 l Schmelzvolumen
- Strom: 120-700 A; Spannung 24-70 V
- Standardtiegel: Graphit
- Kopfelektrode (30 mm/50 mm): Graphit
- Bodenelektrode: Kupfer, wassergekühlt
- Abguss durch Kippen des Ofens
- Temperaturüberwachung an Bodenelektrode, Ausmauerung und Abgas
- Möglichkeit der Set-Up-Modifikation nach Kundenwunsch
Contact person
M.Sc. Fiona Pickart
Top Blown Rotary Converter(TBRC)
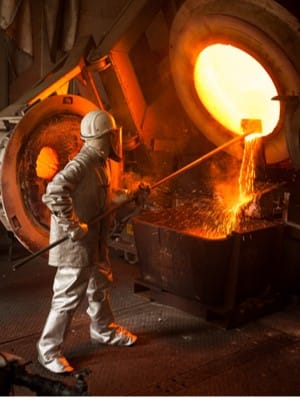
Application area:
- Aluminiumrecycling mit Salzschlacke
- Konverterprozesse durch Sauerstoff auf- oder einblasen
- Schmelzaggregat
- Schlackenarmschmelzen
Performance data
- Rotationsgeschwindigkeit bis zu 10 U/min
- Flexibler Energieeintrag durch luft- oder sauerstoffbetriebenen Erdgasbrenner (max. 500 kW)
- Konverterlanze
- Stufenlos einstellbarer Neigungswinkel des Schmelzaggregats
- Austauschbare Ofengefäße (Variation in Schmelzvolumen und Feuerfestmaterial)
- Gefäßvolumen beträgt 100 l bzw. 1000 l (in Abhängigkeit des Ofengefäßes)
Contact person
M.Sc. Joscha Kortmann
Hochdrucklaugungsautoklav
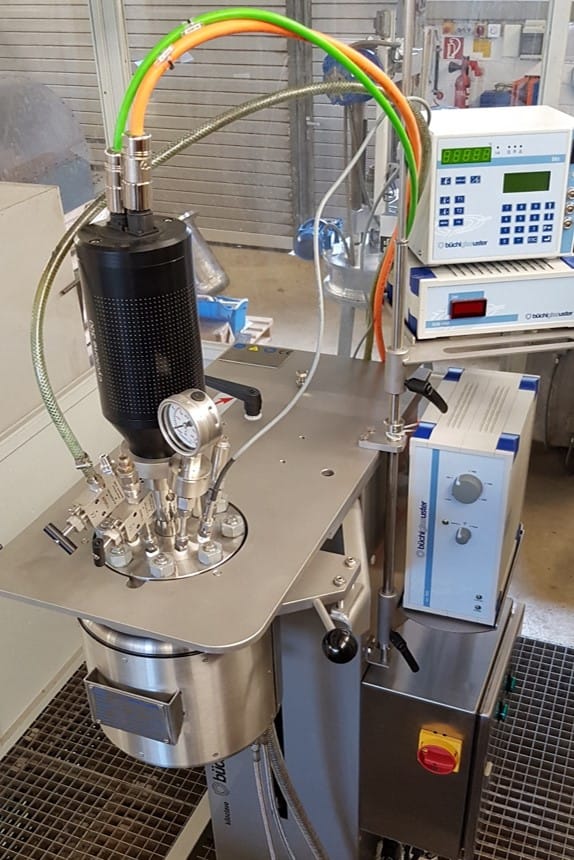
Application area:
- Laugung unterschiedlicher Erze und Konzentrate
- Recycling unterschiedlicher metallurgischen Stäuben
- CO2-Speicherung und Nutzung als Karbonate
- Reinigung von Wälzoxid
Performance data
- Temperatur max.: 300°C
- Reaktionsvolumen: 1-10 l (2 Reaktoren)
- bis 200 bar
- Rührerdrehzahl: 2000 U/min
- Probenentnahme ist vorhanden
- Mögliche Gasatmosphäre: CO2, O2, H2, N2, Ar, Luft
- System für Säuredosierung ist vorhanden
- Online Datenerfassung
Contact person
M.Sc. Dominik Büscher geb. Schmitz
Kaskadenlaugung
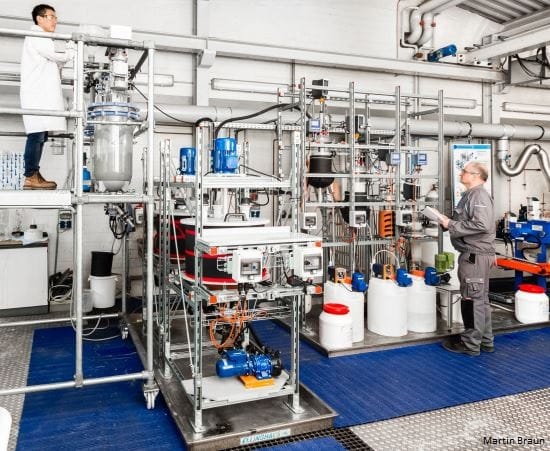
Application area:
- Reinigung von industriell verunreinigigtem Abwasser
- area of application: environmental protection
Performance data
- Konventionelles Verfahren zur Fällung von gelösten Metallen
- Selektive Entfernung mit Hilfe von pH-Wert-Verschiebung
- Etablierte Methode zur Reinigung von metallhaltigem Abwasser
- Neutralisierung mittels Natronlauge oder Kalkmilch
- Vollautomatisierte Chemikalienzugabe über pH-Transmitter
- Online-Überwachungssystem mit Messwerteerfassung
- skalierbare Durchsatzkapazität durch modulare Erweiterung/Erhöhung
- Kostengünstiger Verbrauch von Energie und Ressourcen
Contact person
M.Sc. Dominik Büscher geb. Schmitz
Mikrowelle Anton Paar
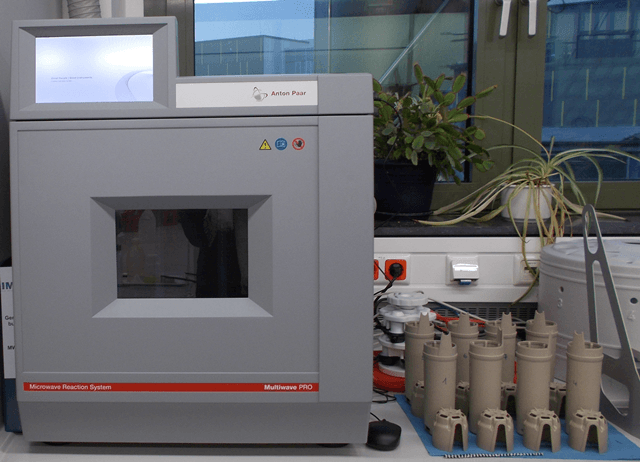
Application area:
- Mikrowellenunterstützte Probenvorbereitung
- Mikrowellenunterstützte chemische Synthese
- Schneller und vollständiger Aufschluss in geschlossenen Gefäßen
- Extraktion mit organischen Lösungsmitteln von organischen und anorganischen Proben unter hohem Druck und bei hoher Temperatur
Performance data
- Stromversorgung: 230V, 50Hz, 3680VA
- Leistung Magnetrons jeweils 850W
- Mikrowellenleistung 1500W
Contact person
M.Sc. Monika Keutmann
Solventextraktionsanlage
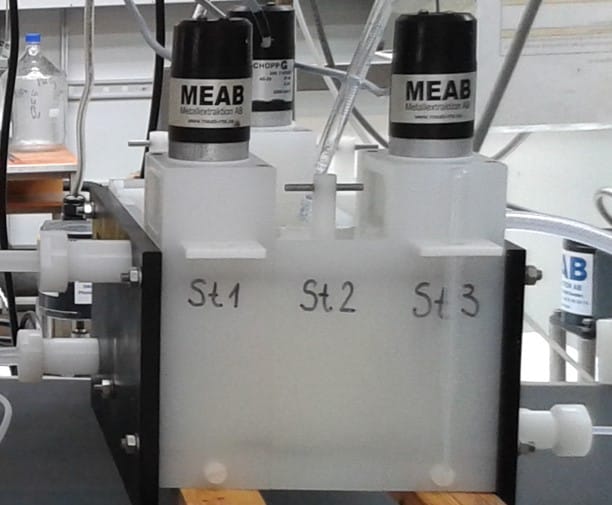
Application area:
Typ: Mixer-Settler
- Hydrometallurgie
- Solventextraktion
- Selektiv arbeitendes Separationsverfahren
- Entfernung von Verunreinigungen
- Aufkonzentrierung der Lösungen
Performance data
- Mixer-Settler Units 0,5
- Kontinuierliche Betriebsweise
- Mehrstufiges Verfahren: insgesamt 5 Mixer-Settler Units
- Einstellbare Flussrate (max. 10 L/Stunde)
Contact person
Priv. Doz. Dr. -Ing. habil. Srecko Stopic
Ultraschallprozessor von hielscher
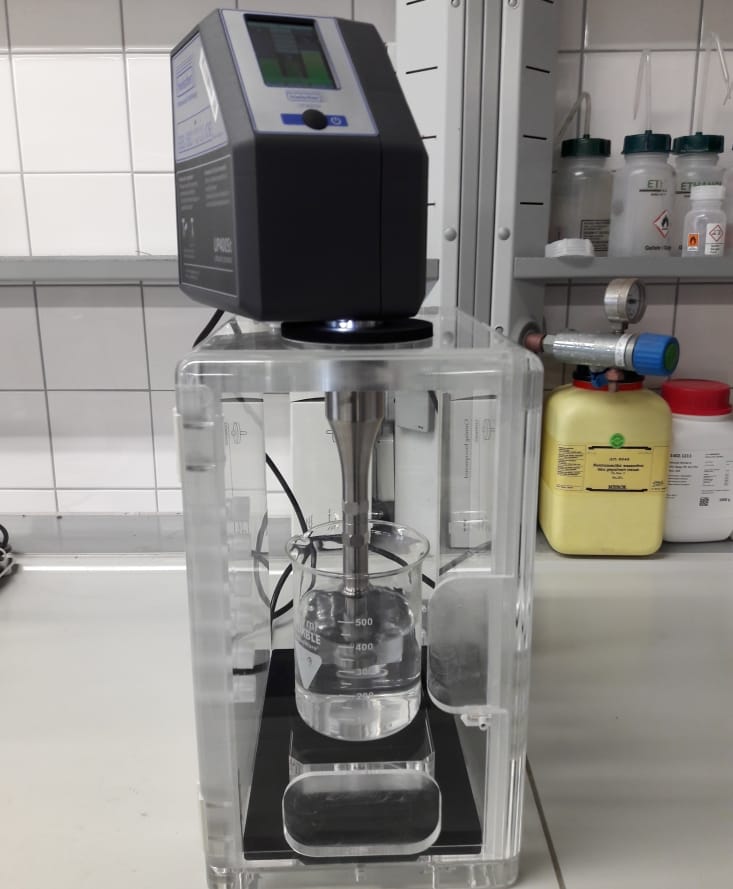
Application area:
- Reinigung von Glasgeräten
- Ultraschallunterstützte chemische Synthese
- Verbesserung der Durchmischungen von Dispersionen
- Entgasung von Flüssigkeiten
Performance data
- Arbeitsfrequenz: 24 kHz
- Regelbereich ± 500 Hz
- Amplitudenregelung 20-100%
- Verschiedene Sonotrodensurchmesser
Contact person
M.Sc. Monika Keutmann
Drehrohrofen
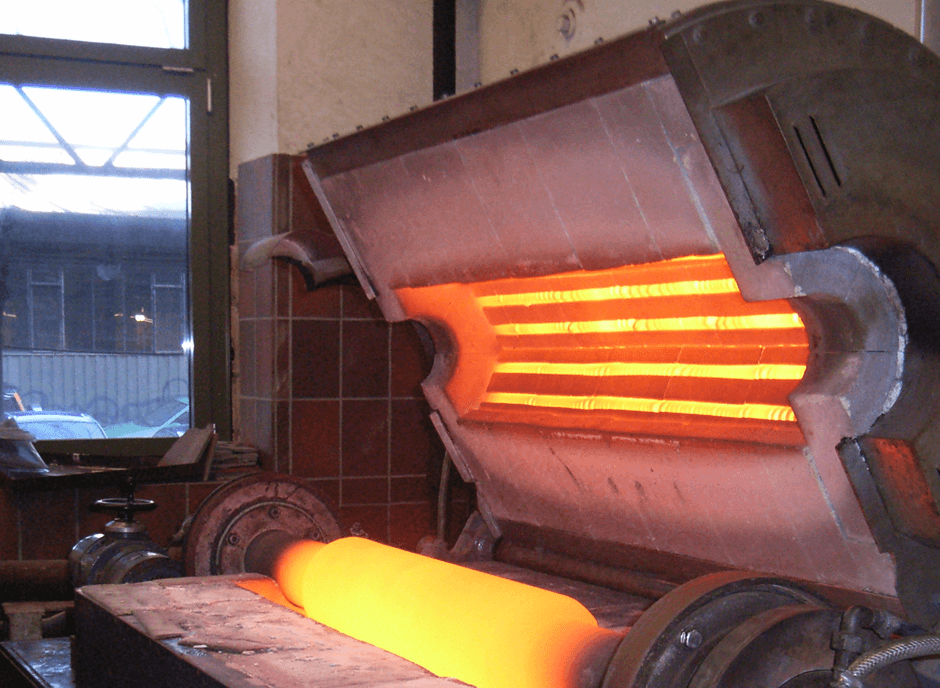
Application area:
- Verflüchtigung von zinkhaltigen Vorstoffen
Performance data
- Arbeitstemperatur bis 1100°C
- Rotation stufenlos einstellbar
- Drehrohre für reduzierende, oxidierende und schwefelhaltige Atmosphäre
- Einleitung von Spülgasen
Contact person
M.Sc. Paul Geller
High temperature vacuum rotary kiln
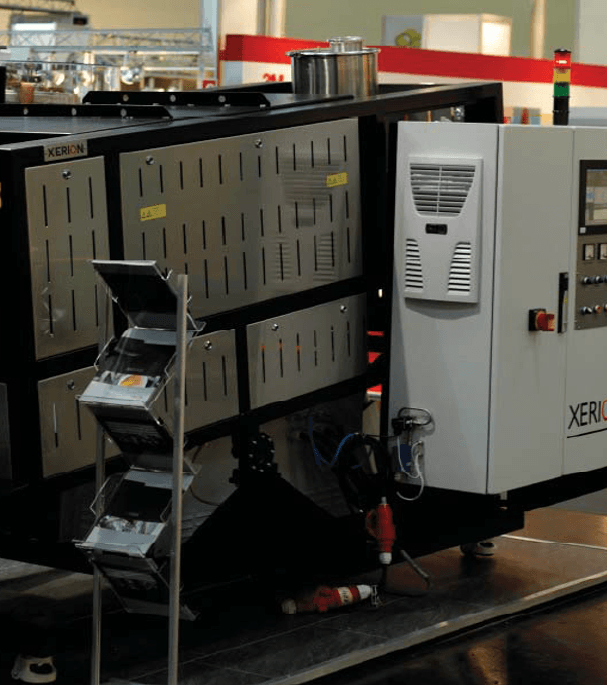
Application area:
- 10 U/min, 10° Neigungswinkel: Verweilzeit von Pulver beträgt ca. 2min (0°C - 1500°C)
- 0 U/min, 0° Neigungswinkel: Kein Materialaustrag (Batch-Prozess) (0°C - 1500°C)
- Keramisches Arbeitsrohr (Tmax = 1600°C) maximale Korngröße von Input-Material beträgt 15 mm.
- Edelstahl Arbeitsrohr (Tmax= 1000°C) maximale Korngröße von Input-Material beträgt ca. 30 mm.
Performance data
- Maximaltemperatur: 1.600°C
- Arbeitsrohre: I) Aluminiumoxidkeramik, Qualität C610, II) Hochtemperaturfester Edelstahl 1.4841
- Innendurchmesser: 150 mm
- Gesamtlänge: 2.000 mm
- Heizung: Heizelemente: Molydändisilicid
- Heizzonen: Drei (vollautomatisch einzeln regelbar)
- Beheizte Länge: 1.000 mm
- Drehzahl: 1 bis 10 U/min
- Neigung: 0 bis 10° (vollautomatisch regelbar)
- Atmosphäre: Vakuum (bis 10mbar), Inertgas (Mit-, Gegenstrom)
Contact person
M.Sc. Paul Geller
Metallothermische Reduktion
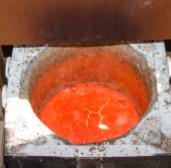
Application area:
- Möglichkeit zur Metallerzeugung aus hochschmelzenden Metalloxiden
- Metallothermische Reduktion mit Aluminium, Magnesium als Reduktionsmittel
- Autothermer Prozess, nur Initialzündung notwendig
- Herstellung von Refraktärmetallen und Vorlegierungen (TiAl, Ti24Al16V, CuCr, NbCr, etc.)
Performance data
- Reaktorvolumen bis 200 l (entspricht ~ 60 kg einer Ti-Vorlegierung als Zielmaterial)
- Geringer apparativer Aufwand
- Schnelle Reaktionszeiten (2 - 20 Min.)
- Temperaturarbeitsbereich (einstellbar über Energiedichte): 1 700°C - ca. 2 600°C
- Fahrweise: Batchbetrieb; Inline-Casting zur direkten Elektrodenherstellung möglich
Contact person
M.Sc. Richard Schneider